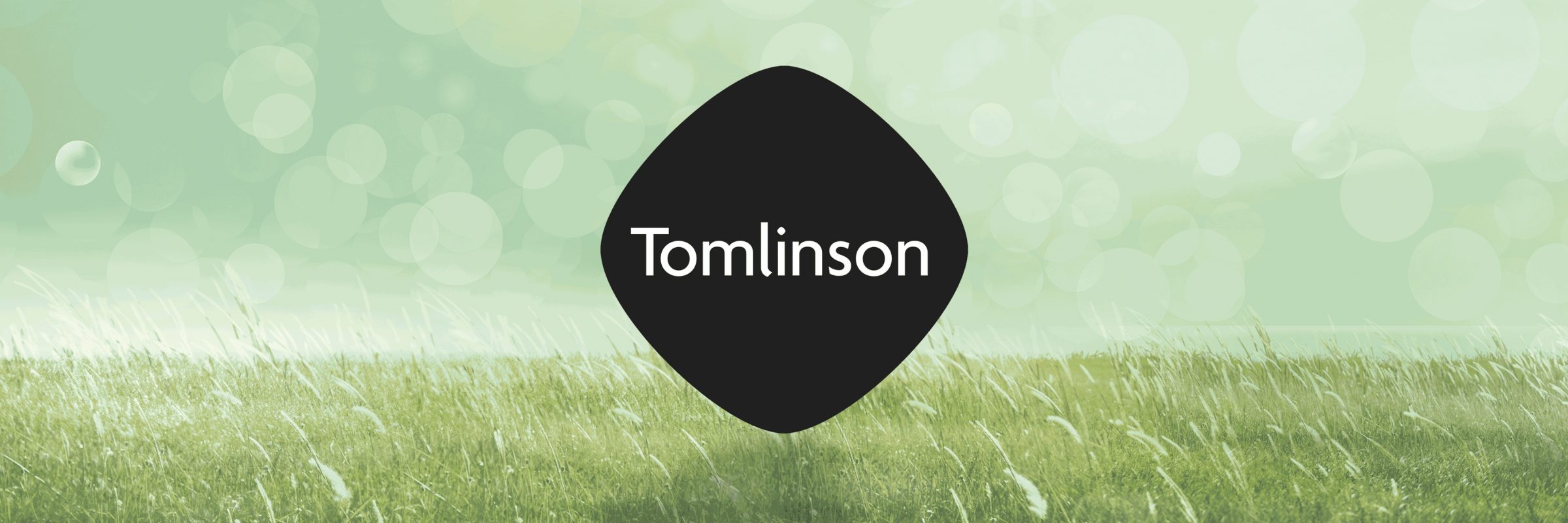
Here at Tomlinson Ltd, we take our environmental responsibilities very seriously. We are dedicated to finding ways to reduce the environmental impact of our production processes while continuing to deliver the high-quality foiling and embossing products we’re renowned for. By regularly reviewing our daily working practices and workplace culture, we endeavour to work in the most sustainable way possible.
Environmental Aims
As a business, Tomlinson Ltd aims to go further than simply complying with environmental legislation. We continuously seek to integrate environmental best practice throughout our company and supply chain by:
- minimising our carbon footprint
- considering the environment when procuring goods and services
- considering the environment in the services and solutions we provide to our customers
- the efficient use of energy and utilities in our business
- reducing fuel consumption
- working with local businesses, neighbours, partners and suppliers to improve our local environment
Waste Management and Recycling
An example of how Tomlinson’s actively work towards a sustainable future is our relationship with local Leicester-based scrap metal and waste disposal firm, T. Watts Waste.
T. Watts Waste continually invest in the latest segregation equipment to increase the percentage of materials that can be recovered from our waste; waste that, previously, would have been bound for landfill. They collect and recycle glass, cardboard, paper, wood, metal and many plastics, and a large volume of that waste goes for Refuse Derived Fuel (RDF). Both Watts and Tomlinson are committed to minimising the quantity of waste directed to landfill and attain around a 95% recycling rate.
The metals Tomlinson’s work with are fully recyclable and all waste metal generated from trimming, cutting and etching the dies we produce is captured and recycled. In the same way, chemical waste derived from the etching of magnesium dies is safely collected via a serviced waste management system before being disposed of responsibly by professionals.
Smarter Production Processes
Over the last twenty-five years, Tomlinson’s has invested heavily in an array of high-spec tech, including the latest in CNC milling machinery and computer-to-plate (CTP) technology. Our CTP capability has eliminated the need for film to be run - a process previously required to expose an image to a blank plate before etching.
In addition, our perpetual investment in digital cutting equipment has seen Tomlinson’s product offering evolve. Advancements in CNC technology and the fine tooling now available mean that delicate detail previously only replicable etched in copper (a process requiring the use of Ferric Chloride) can now be machine-cut far more cleanly in brass.
From making the most efficient choices of the resources and production processes we use, through to preventing pollution, minimising waste and the promotion of our recycling policies to our staff and suppliers, Tomlinson Ltd constantly strives to make our busy die-making facility as safe, efficient and environmentally responsible as it can possibly be.