
Ginger Singh-Kauldhar
Optimising Magnesium Etching Capabilities
At the end of 2017 Tomlinson replaced it’s larger aging and unreliable magnesium etching machine. It was replaced with a new top of the range 200 litre Stoma machine, which in turn provided an opportunity to make many process improvements. To produce good dies, magnesium etching requires process parameters to be tightly controlled. During the process, nitric acid and other special chemical additives strike the magnesium workpieces at high velocity. This causes an exothermic reaction to take place and it is essential that a fine balance between temperature, chemistry and fluid turbulence is maintained. To add further complications, different products require different process limits. The process criteria for a 0.5mm deep embossing die is very different to those required for 3mm deep flat foiling die. Making matters even more difficult, the chemical composition of the etching liquid changes over time and eventually it has to be replenished. It is a complex process to control if consistently good dies are required.
Because the new Stoma machine was potentially so capable, we were able to embark on an improvement project that employed lean manufacturing tools borrowed from the automotive industry. We extensively identified the causes of poorly etched dies, determined what process conditions needed to be maintained to make only good dies, then finally what controls we needed to put in place to ensure that bad dies would not be manufactured. The investigation and analysis took a number of months but at the end we had designed and installed a robust process control system which allowed us to operate the etching machine to full potential. In addition we also had a much deeper understanding of the etching process, from the function of individual chemical components to the mechanical operation of the machine itself. Today, we have process controls in place that have enabled us to easily train new staff to etch but still be confident that etching standards across a very broad range of dies are maintained.
During this period of investigation, we continued to use our other smaller machine, which had been upgraded many times over the years. However, it became very apparent that it’s capability was a limitation - it was not so versatile and it required frequent “nursing” which restricted our etching department’s flexibility. We purchased another Stoma machine which has now been in use for a few months. Because of the work that had previously been carried out, it was an easy task to unlock the machine’s capacity.
Tomlinson’s production director, Jon Colbert says “the work that we carried out to improve the quality of our process and product, ensures that we can fully realise our investments. Not only that, but these two new machines along with our systems have increased capacity beyond what we originally thought was possible.”
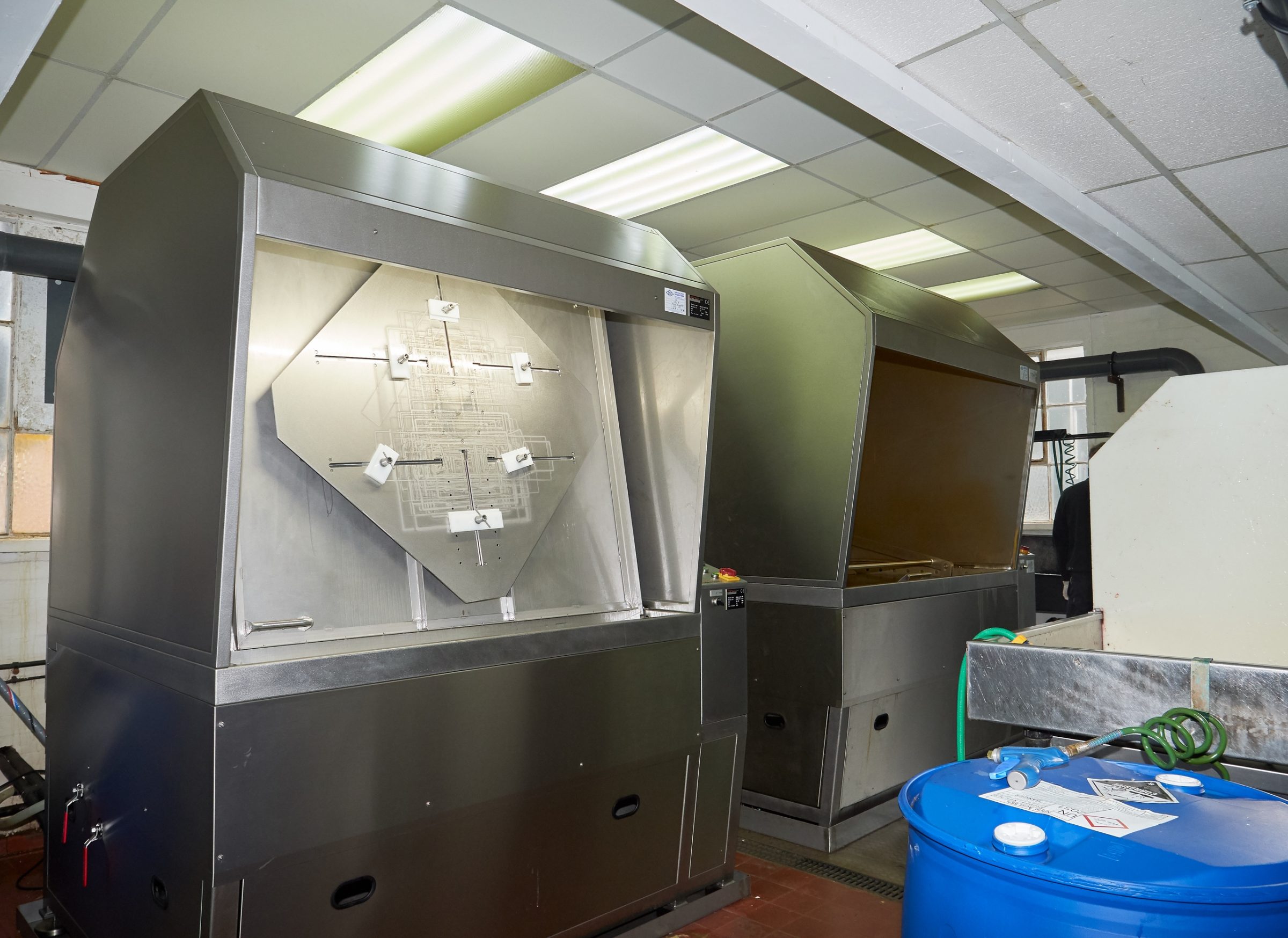